With the success of our Billet Clutch Fork for the VA WRX and various other Subaru models, we decided to take the development process one step further.
We designed and developed a Forged Clutch Fork, which is even stronger than our machined unit. These new forged units are produced from the same material; but, being forged, it is squeezed into the shape which leads to superior grain properties. We then heat treat the forks to a hardness of 26-32 HRC (very hard) and after that cryo treat them for superior physical properties. The units finally are black oxide coated for rust resistance.
What is forging?
Instead of machining the unit from a solid piece of material, an ingot is heated and then under extremely high pressure, is formed into shape. This is much less wasteful in the long run and when we are dealing with large quantities, the extremely large upfront tooling costs can be justified.
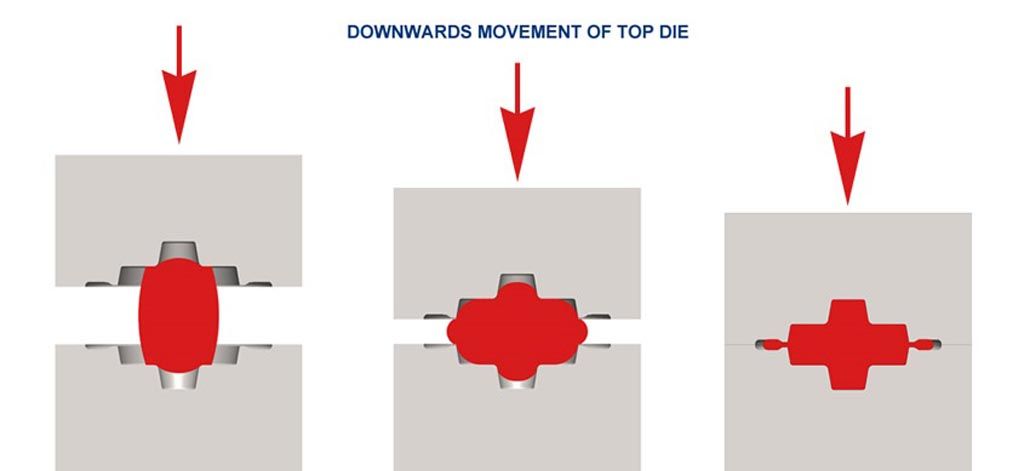
This process improves the physical properties of the product through the microscopic grain structure which is invisible to the naked eye. See below for a picture to better describe this.
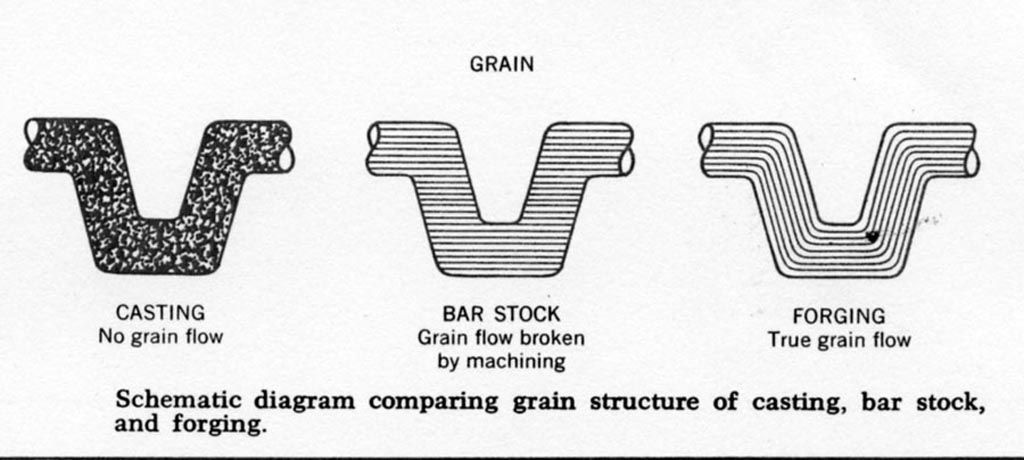
If you are a real nerd like us, check out some videos on YouTube! The process is breathtakingly impressive. Forged cranks, rods, pistons, etc are all produced in this fashion and then typically finish machined, as were our forks in select areas.
What does this all mean to the end product?
As shown below, we can clearly see the severe decrease of stress concentration moving from OEM to machined, to finally forged.
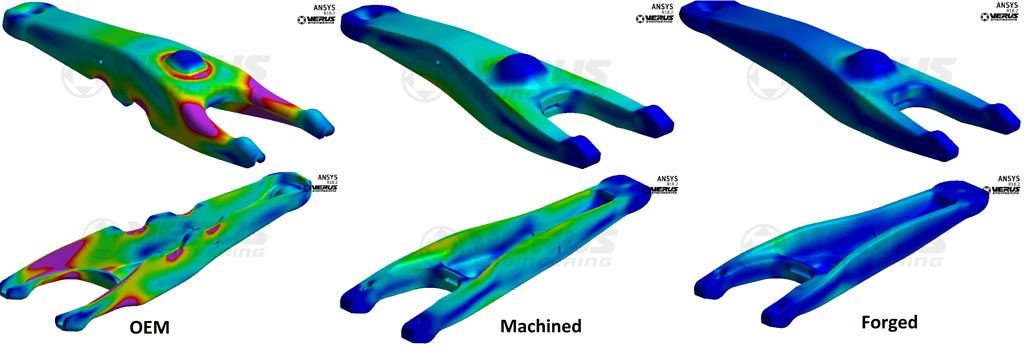
All graphs are set the exact same, with yield strength at the limit of the color code (red). Warmer colors, like red and purple, show areas over yield strength. The cooler colors, like deep blue, represent areas of low stress. As you can see, the fork has improved again in strength as a result of the forging process when compared to the machined and OE component.
If the machined units were doing fine, why upgrade further?
We continually had a hard time stocking the clutch forks and our costs were higher than we cared for. We decided to front the large tooling costs in an attempt to alleviate stocking problems and reduce our cost over the decades we hope to sell the clutch fork. Basically, instead of thinking short-term (machined) we are looking longer term *while producing a superior product*.
Absolutely *nothing* was wrong with the machined unit and to date, we have not had a single unit failure.
In conclusion, we hope you enjoyed a small in-depth informative blog about the evolution of our clutch fork. Please let us know if you have any questions or concerns.
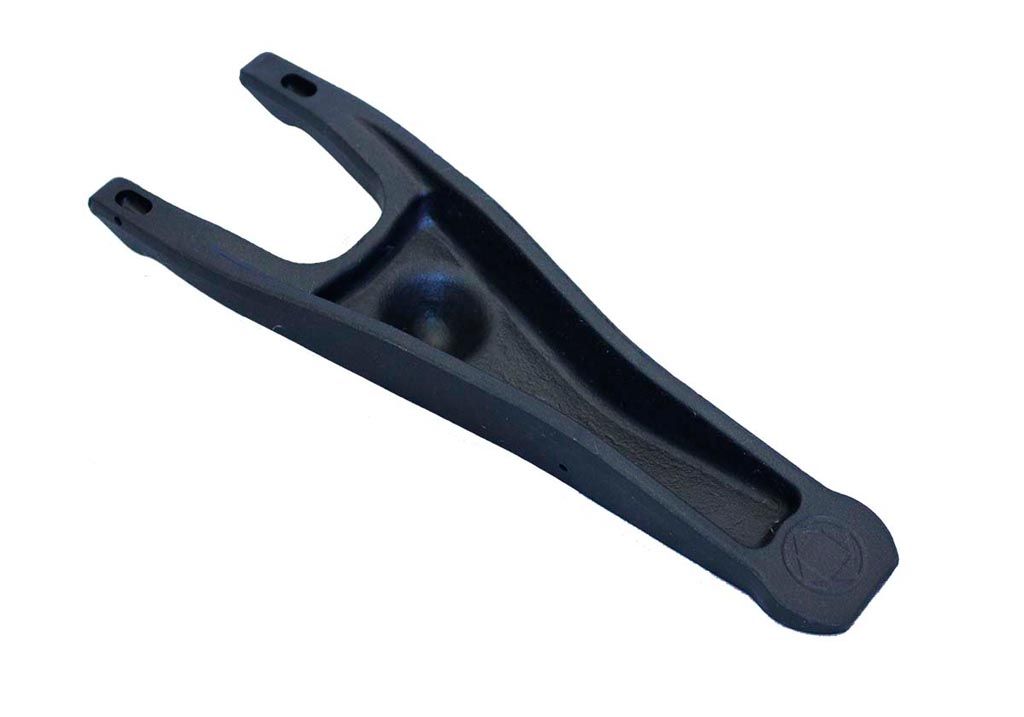
VA WRX Clutch Fork Evolution