With the advent of scanning, reverse engineering for engineers got significantly better and easier. This leap forward in technology allows us, as design engineers, to do things that would otherwise be impossible or very difficult. However, this does not mean that it is necessarily easy or quick to design parts from scan files and that is the reason behind this blog, to show you a behind-the-doors look at how we do, what we do, on a daily basis; and the amount of time and effort it takes.
What is scanning?
3D scanning an object, part, or car, is a way to capture the 3-dimensional object from the real world and capture it into the computer world. Scanners do this by creating point clouds, which are exactly what it sounds like; clouds of points.
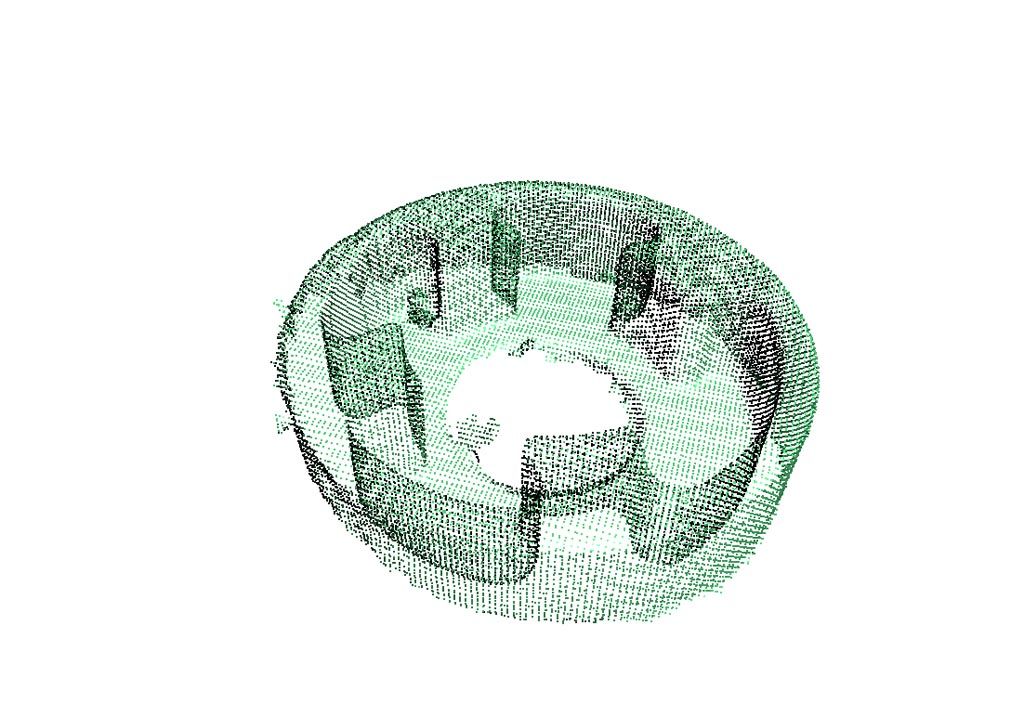
From these point clouds, the software can facet and join these points to create faceted geometry. Note that the below picture is *not* smooth, the data is currently a representation of the actual component and a good one at that, but it is not smooth. CAD data has parametric equations governing the actual file created; while scan data has no governing equations.
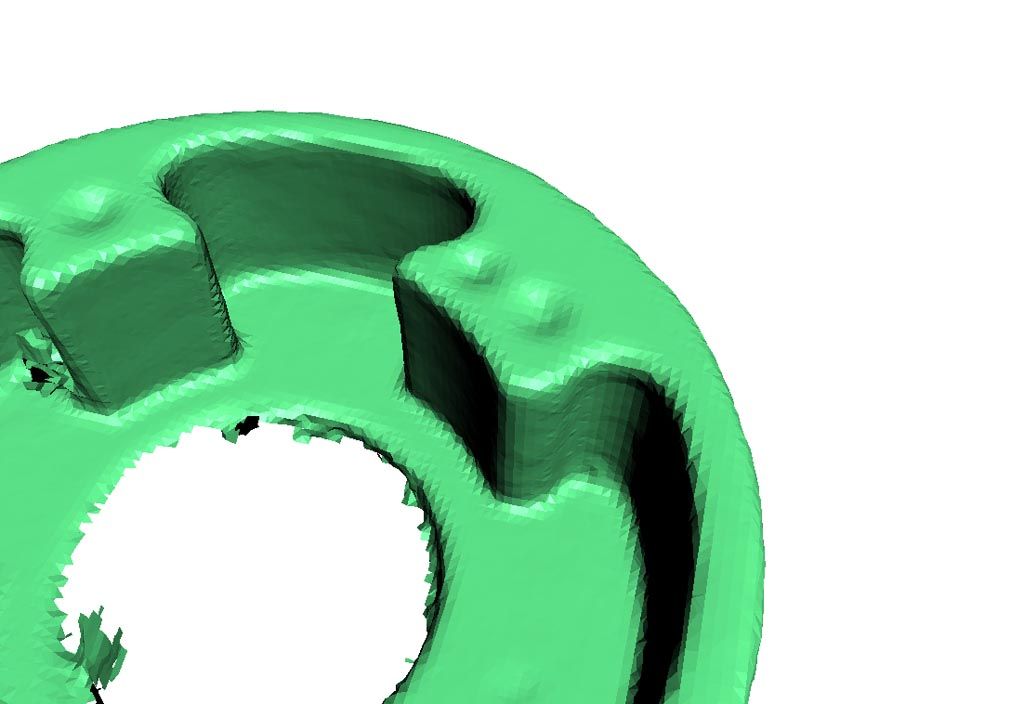
FAQ:
I’m going to start with a few FAQ/misconceptions, and after go more into depth regarding working with and designing with scan data.
Q: Once you scan an object, isn’t it just a part, in CAD?
A: No. Scan data is a point cloud. It comes through in CAD as faceted geometry, which is sharp and jagged, as well as infinitely thin.
Q: So when you scan a part, you cannot print and machine directly from that?
A: No. Scan data, once again, is infinitely thin facet geometry. For a part to be machined or printed, the part needs to be solidified.
Q: Isn’t their software that can do this for you?
A: Yes, there is some extremely powerful reverse engineering software. These softwares generally start around the $25k/year for a license. Even then, these softwares require human input to completely decipher the information given in a scan file. The reverse engineering software does decrease time involvement; but, it doesn’t create solidified geometry automatically either.
Q: So what is the point of scanning if you can’t really use it?
A: Without scanning, some designs would be impossible to reproduce or extremely time involved to design components off of. Scan data gathers a lot of data quickly, where reverse engineering with a tape measure and a pair of calipers measures a single data point at a time.
Q: With scan data, that’s all you should need right? The parts designed will be accurate.
A: In a perfect world, yes. However, scan data doesn’t always pick up specific small details at times which can lead to difficulty designing and reverse engineering specific components.
Where does scanning fall short?
Scanning objects with deep recesses, like holes, do not come through well. This is a result of the scanner not being able to ultimately see deep into the pocket. This makes designing parts with accurate hole locations difficult at times. This is one of the largest misconceptions with scan data; that once you scan it, you have all the data and it will be easy to design from.
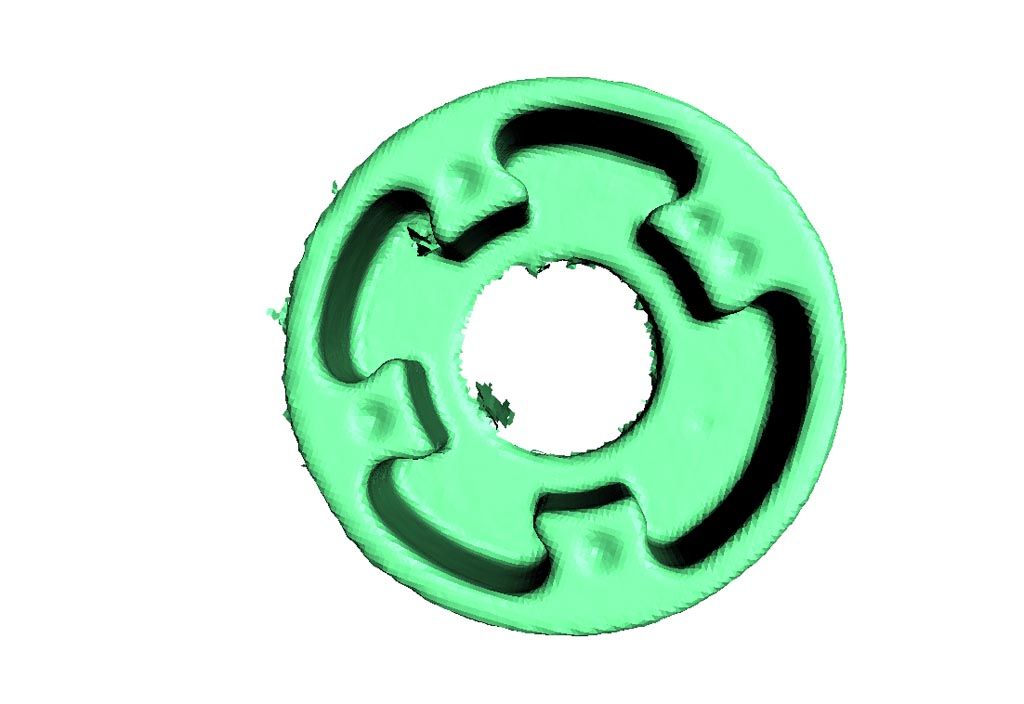
How long does it take to scan a part?
Depending on the object, as quickly as half an hour, to as long as 6-8 hours. To do a small piece, like what I have been showing photos of, it took about 30 minutes to scan, fuse the multiple scan files, and output a surface file. To do a vehicle, it takes multiple hours to do the physical scanning and then multiple hours to stitch together the scans and fuse them. Keep in mind that fusing the scans together just creates an infinitely thin single feature; to run CFD or use that data for anything meaningful; we still need to create a solidified model from that data.
What do you mean infinitely thin surfaces?
The surface that is from the scan data, has no thickness. Design engineers call this a surface, but to a typical person, a surface may appear to have a thickness. Even a piece of paper has a thickness, but in the CAD world, a surface has no thickness. At times, this surface can be easy to work with and we can possibly thicken it. Most times, the scan surface is impossible to work with and needs significant work to thicken.
How long does it take to create useful CAD from Scan Data?
This ranges widely on each project. To give you a rough idea, the piece posted multiple times in this blog took about 2.5-3 hours to design a CAD model. An entire car; takes roughly 3-5 working days to solidify and get ready for CFD analysis.
Conclusion:
While scan data is an impressive and groundbreaking R&D process; which allows us as engineers to do things that would otherwise be impossible, it does not mean that the process is easy by any means.
Scanning 101, FAQs, and Misconceptions