Most people automatically assume that aftermarket radiators are superior or better than OEM or the more expensive units on the market. Like most things; you generally get what you pay for and higher-end radiators sport superior cooling capabilities while the lesser alternatives generally cool worse than OEM. We will be looking at photos from two different cores at Verus today, a low-quality unit and a high-quality unit (typically used in all forms of Motorsports) and comparing the two units. We will only be looking at the cores primarily; as this is where the majority of the heat transfer takes place. The primary details we will be looking at will be the brazing quality, the tube construction, and the fin construction.
We are pulling from information from past employment where we supplied all forms of motorsports with high-quality cooling components; from IndyCar and
Core Make Up
I will be using verbiage that may not be common knowledge for some readers. Below is a photo with arrows pointing out the three main components that make up a radiator. They are the header plate, the tubes, and the fins.
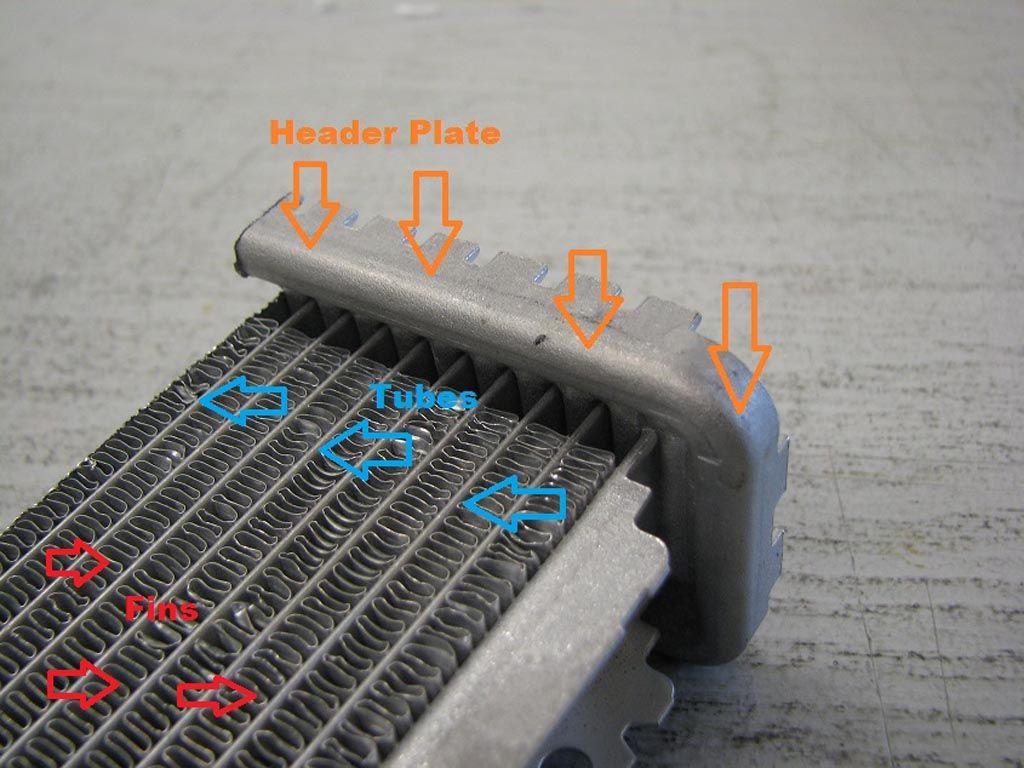
Brazing Quality
Brazing is the technique of joining metal together by melting and flowing a filler metal into the joint. The filler material, called clad, will have a slightly lower melting point than the base metals. This is how aluminum radiators are constructed
There are two main braze joints on an aluminum radiator, from the radiator fins to the tubes; and from the tubes to the header plate. The quality of the actual clad varies as well and can influence both strength and heat transfer.
Tube to Header Plate:
This
In our case, both cores are brazed. However, the header plate on the high-quality core is formed significantly to increase the tube to header plate surface area; resulting in a much stronger joint. The below images both point this out on the high-performance radiator. OEM and high-performance radiators do this to dramatically increase longevity as the tube to header location
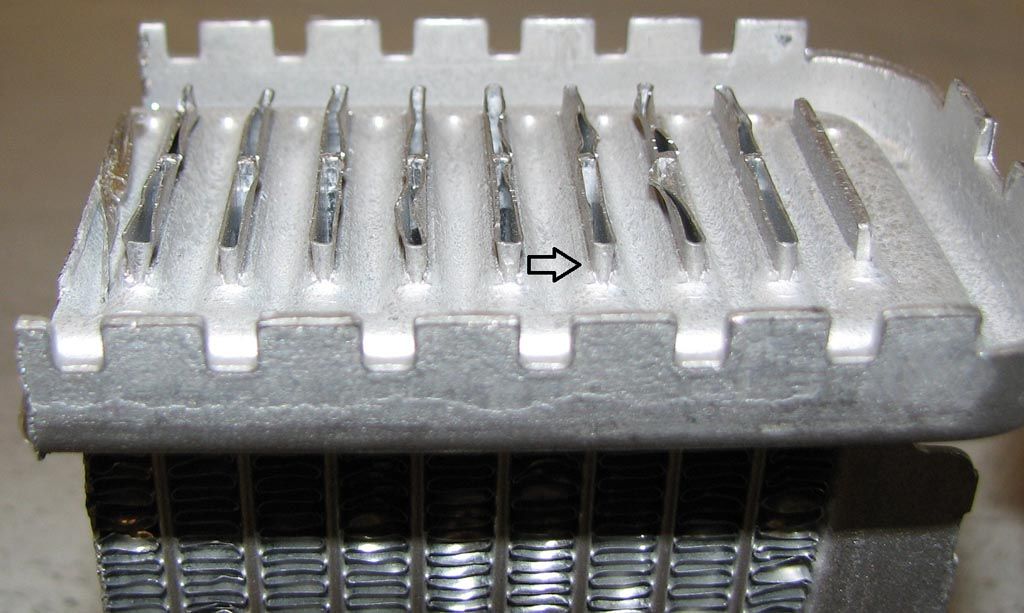
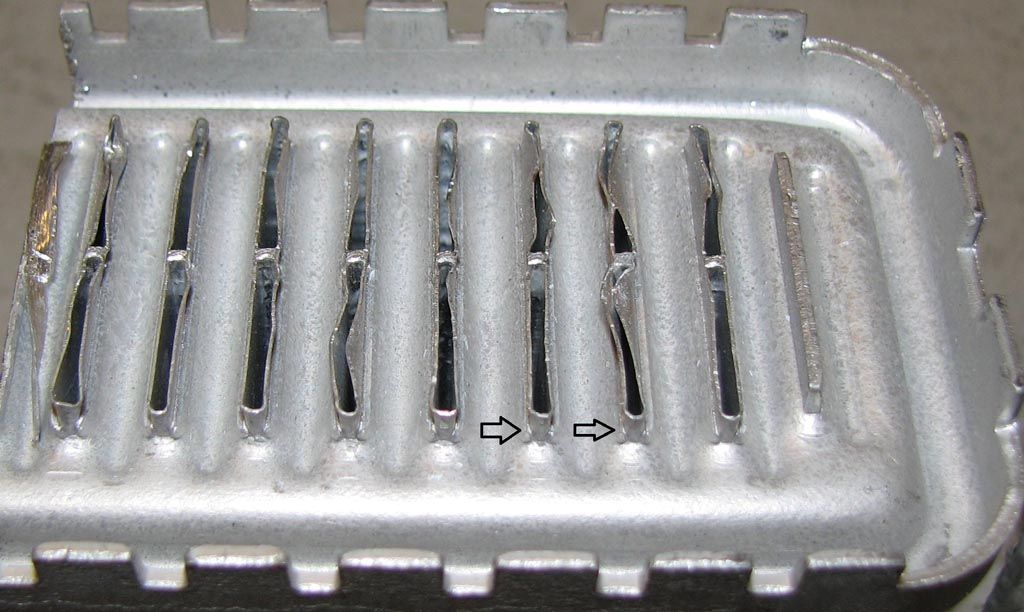
Fin to Tube Joint:
This
In the below photo, I was easily able to pull the tube from the fin joint on the low-quality core. I could have skinned the tube from the entire fin row if I kept pulling. I could not separate the tube from the fin on the high-quality core. I pulled with greater force and less damage occurred. This is a result of superior clad, brazing quality, and overall better processes.
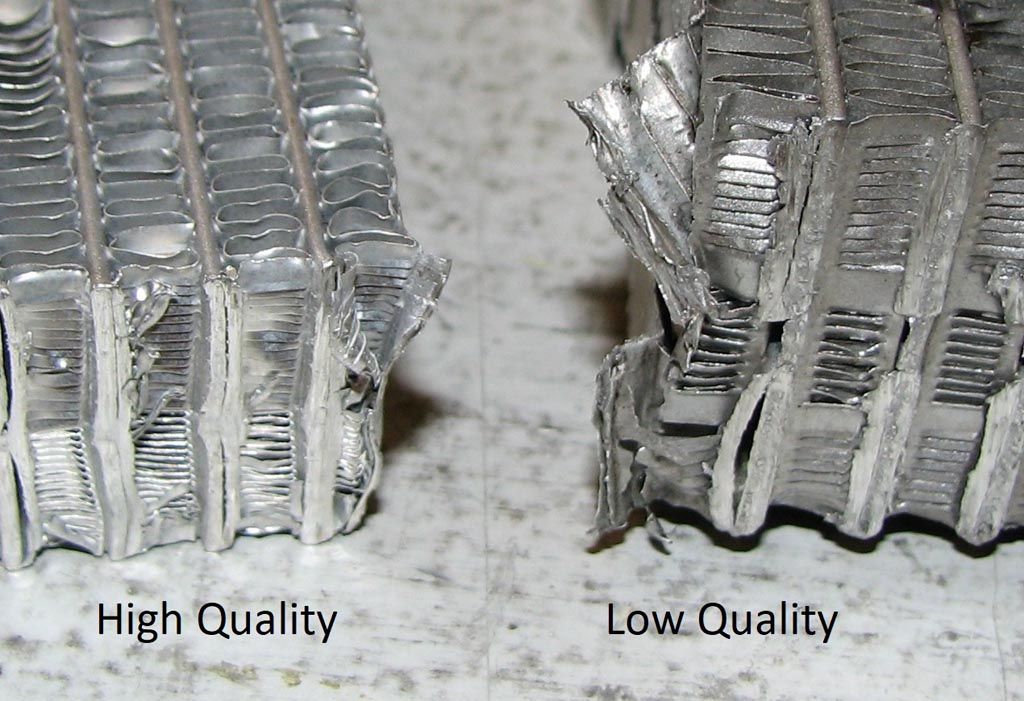
Tube Construction
Tube construction is important for both cooling and strength. Material selection varies as does the actual shape/profile of the tube and thicknesses used. We did not test material
Initially, you can see that the lower quality core is a twin row vs. a single row for the higher quality core. This does not necessarily reduce performance but it does increase thickness while not increasing surface area, which is not a positive thing. The high-quality core is taking advantage of every available mm of space.
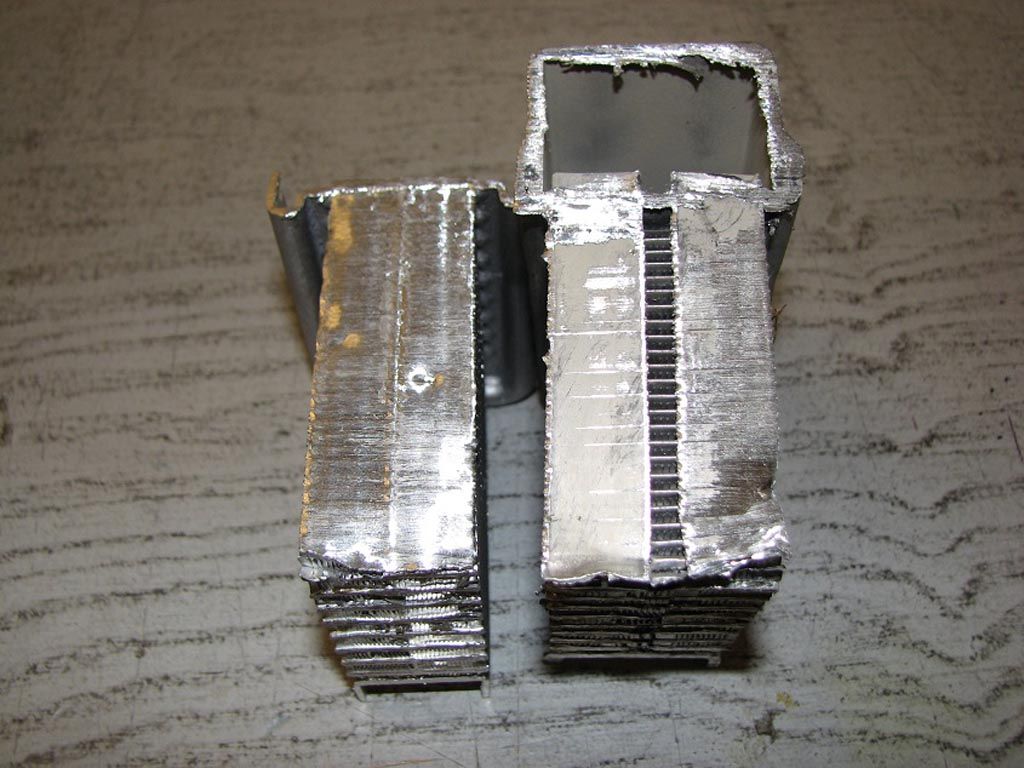
Tube Thickness:
Let’s take a look at the dimensions of the tubing itself. The higher quality core has a tube thickness of 0.1mm, while the lower quality core has a tube thickness of 0.21mm. This is a massive difference and greatly affects the heat transfer of the core.
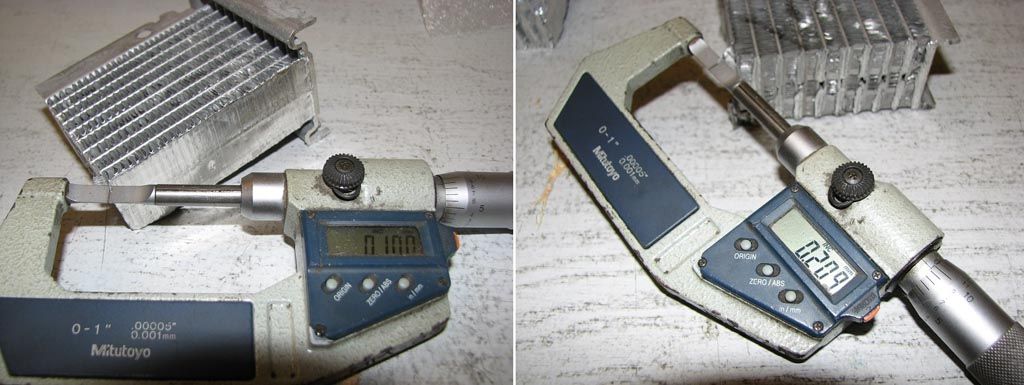
Tube Height:
The tube height is also different, ~1.72mm height for the lower quality core and ~1.52mm for the higher quality core. The higher the tubes, the more blockage on the air side the core sees; however, better water-flow results as well. The issue here is that with the wall thickness being 0.2mm for the lower quality core; that results in an internal tube height of 1.32mm, the same for both cores. The higher quality core will have a better air side pressure drop as a result and improved cooling.
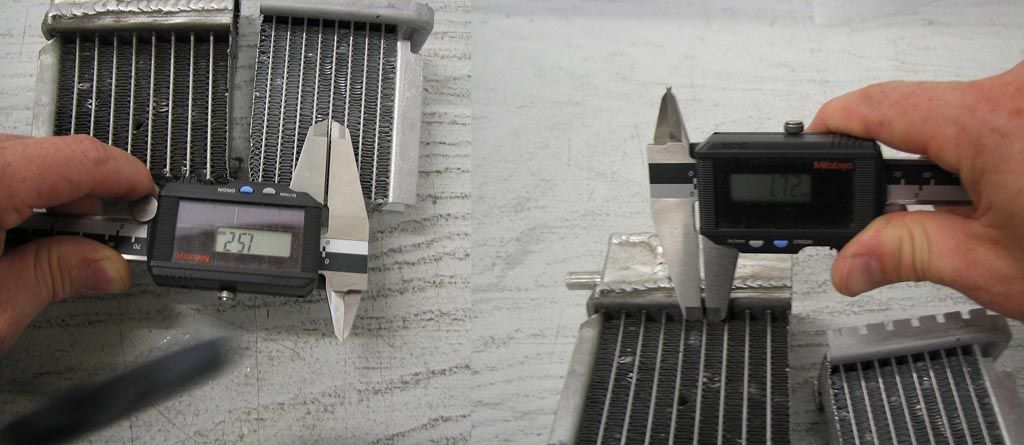
Fin Construction
The fins are where the core exchanges heat with the ambient air
Fin Thickness:
Initially, we can measure the fin thickness. This is easy to test with micrometers and shows just how
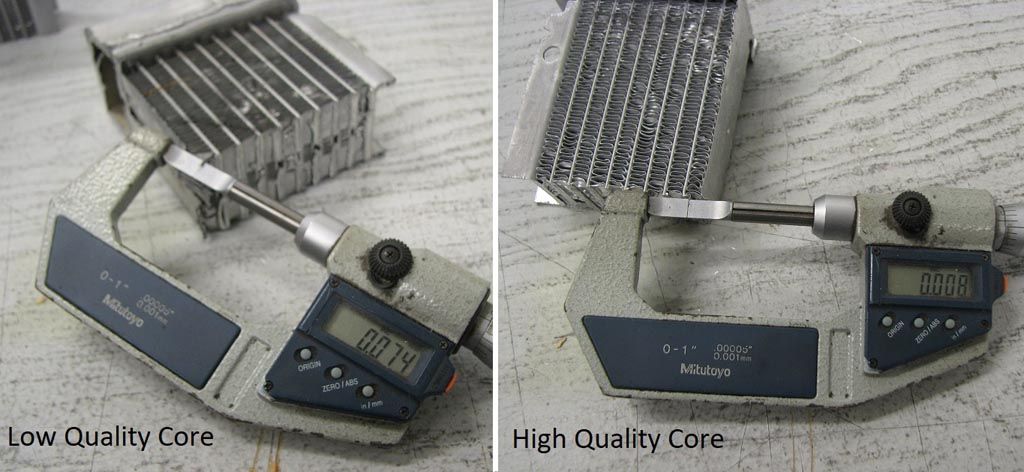
The fin heights are also quite different. Larger fin heights will allow more airflow through the radiator (reduced pressure drop) but that also means you get

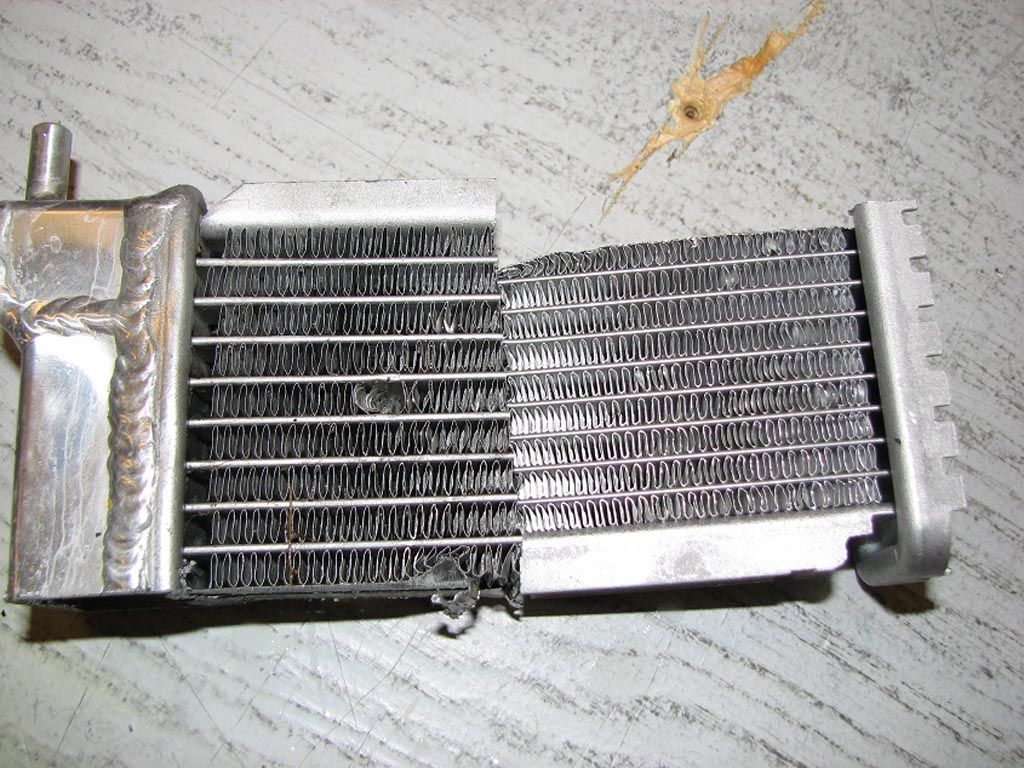
Louver Detail:
The individual louvers in the fin, which tabulate and greatly improve heat rejection, are arguably the most important piece of the radiator core for performance. Performance varies greatly based
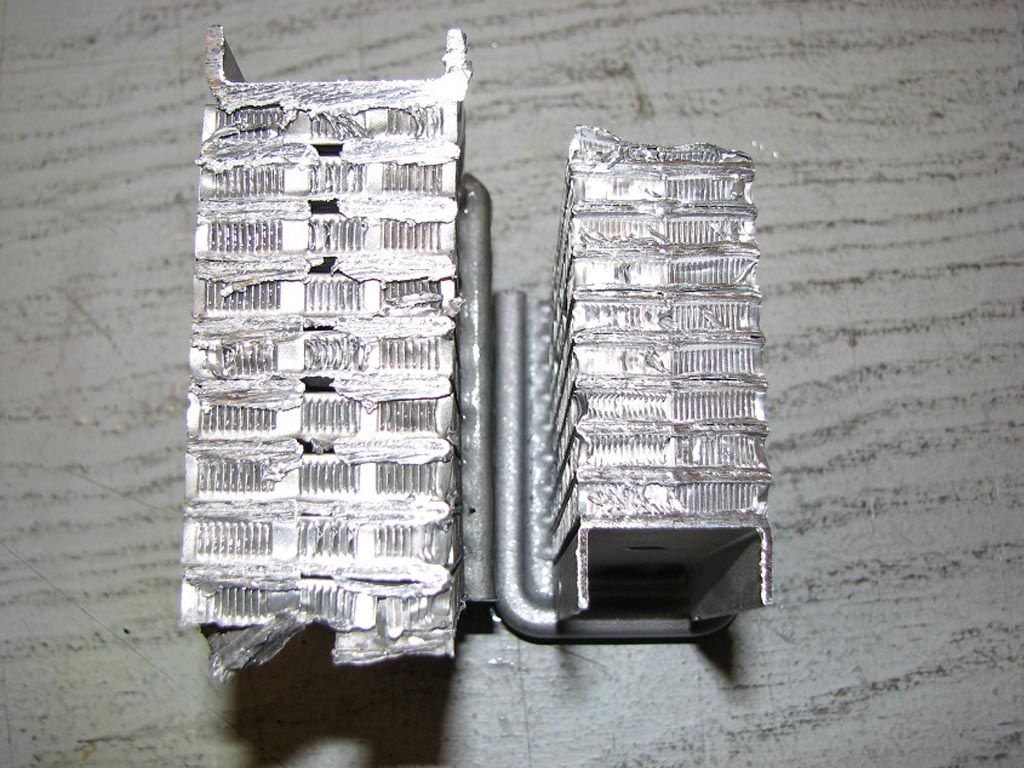

Not All Radiators Are Created Equal