This will primarily be a discussion for forced induction applications; there is not much that can be
Why does the air heat up?
Compressing air via a turbocharger or a supercharger will cause the intake air to heat up. This is due to the ideal gas law equation PV=nRT. If volume (V), amount of moles (n), and the ideal gas constant (R) all stay the same (which in our case, they do), as pressure (P) is increased, the temperature (T) has to increase as well to keep the equation equal. There is no way
What does this mean?
Air at higher temperatures is less dense
then lower temperature air. A denser (colder) charge increases the number of air molecules that make it into the combustion chamber on the intake stroke, more air + more fuel = more power. So the opposite is true with hotterair and thus reduced power and performance are realized.Disregarding that higher temps can cause pre-ignition/detonation and reduced timing as a result, for every 10
degrees F that the intake air temp (NOT ambient air temp) increases or decreases, a resulting ~1% in horsepower is gained or lost.However, if we do consider that high temps can cause pre-ignition/detonation, then power can suffer significantly and engine damage could occur.
How can we keep the air cool?
Conventional Systems:
Air to Air (A2A) charge air coolers
These would be the large front mounts that we all love. Other packages have these located in side-pods, in the rear, and up top in air ducts. The charge air flows through

OEM Style Tube and Fin
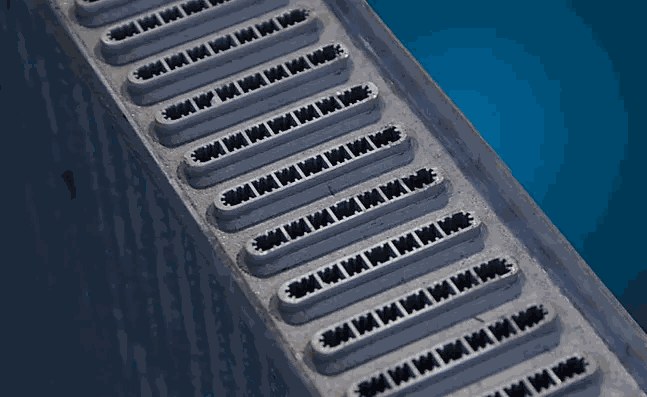
Extruded Tube and Fin
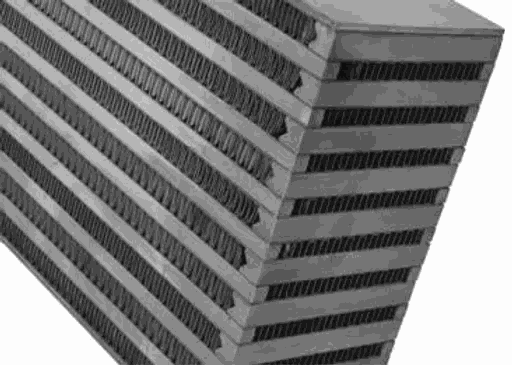
Bar and Plate
Positives:
Extremely simple design and operating principle
Not much can go wrong with this system. Leaks would reduce performance but not cause anything catastrophic to occur.
Costs are generally reasonable with the lower level construction cores.
With higher level cores (think 4 figure pricing) and adequate airflow, near ambient
temperatures, can be reached.
Negatives:
Impossible to cool temps below ambient
Blocks airflow to the radiator and condenser.
Some variants, typically the cheaper ones, are extremely heavy.
The cheaper cores are generally not efficient, but still, get the job done.
Performance is highly dependent on airflow.
Air to Water (A2W) charge air coolers
These are the intercoolers found inside the intake manifolds of some OE cars, Edelbrock’s s/c, Cosworth’s s/c, and Innovate’s s/c. With the use of its own cooling circuit, these can be placed in confined spaces and are generally used to cool the charge air temperatures from a
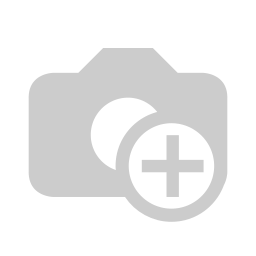.png?access_token=e1f51dc4-cd19-4bd7-9eb8-3e14bb8517fb)
In Plenum Intercooler, ZR1
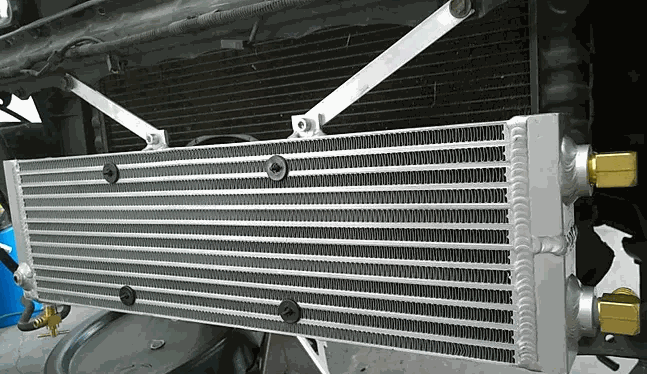
Low-Temperate Heat Exchanger
Positives:
Ability to be packaged in small spacing and placed within the intake manifold itself.
Great for drag cars when used with ice, which can reduce air temps below ambient.
These can reduce pumping losses from reduced tubing and bends.
The intercooler portion itself can be much smaller than an A2A and still reduce air temps drastically.
Less impact on the radiator cooling as the heat exchanger is generally very thin.
Negatives:
These systems are more expensive as they involve more components.
When used without ice, air temps will be higher than a properly sized A2A.
While unlikely and uncommon, they can leak water into the engine.
Less dependent on airflow as the heat exchanger can be placed remotely and a fan used to pull air through them.
Less Common, Non-conventional Systems
Water Injection
By injecting a small amount of water into the intake tract, the water (preferably vapor) can turn to steam and with it, take a significant amount of energy out of the air charge. Water’s high latent heat of evaporation makes it a great fluid to absorb the energy and thus heat from the inlet air. This change in phase (water vapor to steam) is the key to its success. This system can be used in cases when an intercooler is not enough to cool the intake charge.
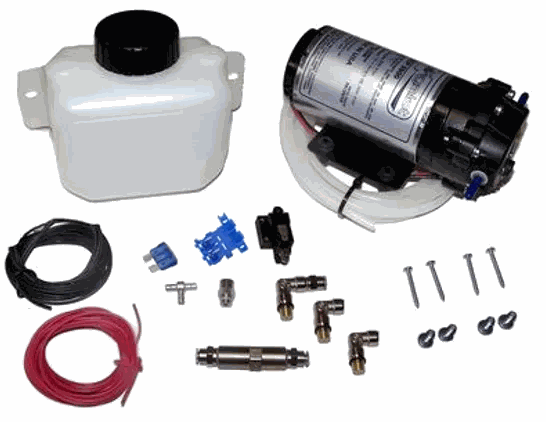
Water Injection Kit
Positives:
Increased knock resistance
Reduced inlet charge temps
Can produce slightly more horsepower
Negatives:
Maintenance
Cost of the system
Have to remember to fill the reservoir
Possible failure point (wouldn’t be significantly destructive if it fails though)
Methanol/Alcohol Injection
Methanol exhibits two main differences from water when being injected into the intake stream. One, methanol is a fuel with the octane rating of ~109 RON, which will greatly increase the knock resistance. The other difference being methanol evaporates at a much lower temperature
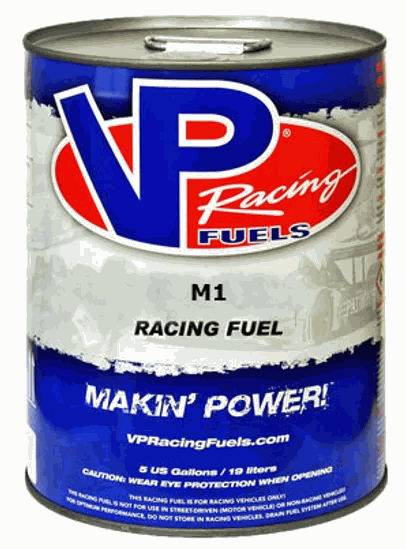
M1 Methanol Fuel
Positive:
Increased octane, reduced knock threshold
Ability to run more timing
Ability to run more boost pressure
Reduced air temps
Negatives:
Added costs (system and the fuel)
Remembering to fill the reservoir
Potential failure point that will ruin the engine
Calibration challenges
Non-Intercooled Applications:
Some vehicles, generally drag cars, do not need intercoolers due to the primary fuel that is used. These vehicles run on either alcohol, methanol, or nitro-methane. For reasons previously discussed, these fuels can cool the intake air beyond that of an intercooler, rendering the use of one obsolete. Ethanol (E85) reduces the need for
Conclusion:
We recommend the use of the conventional systems listed above as we share a similar mindset to the OEMs. These systems work well and if designed properly, you won’t need the use of chemical (fuel)
As always, please let us know if you have any questions and we will do our best to answer.
Charge Air Cooling