Verus Engineering is heading to the wind tunnel to test and validate some of our wings! This is quite exciting for us and we wanted to take a quick moment to discuss what we plan on testing and the magnitude of the wind tunnel testing. We still believe that CFD is the more cost-effective and appropriate approach for our daily R&D, but this wind tunnel test will allow us to ensure our CFD setup is accurate to what happens in the real world.
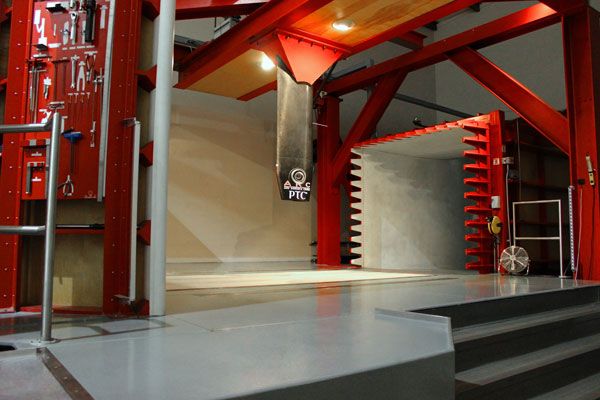
Why are we going to a wind tunnel?
One word, validation! Validating our CFD analysis to a controlled real-world simulation will allow us to better understand and dictate the accuracy of our CFD analysis. While we have validated some of our CFD to strain gauge measurements, coast down tests, and various other real-world tests; we have never been able to validate to this high degree of accuracy. Validating our wing CFD to a world-class wind tunnel will ensure our setup within ANSYS is correct and that the results we publish are accurate to real-world results.
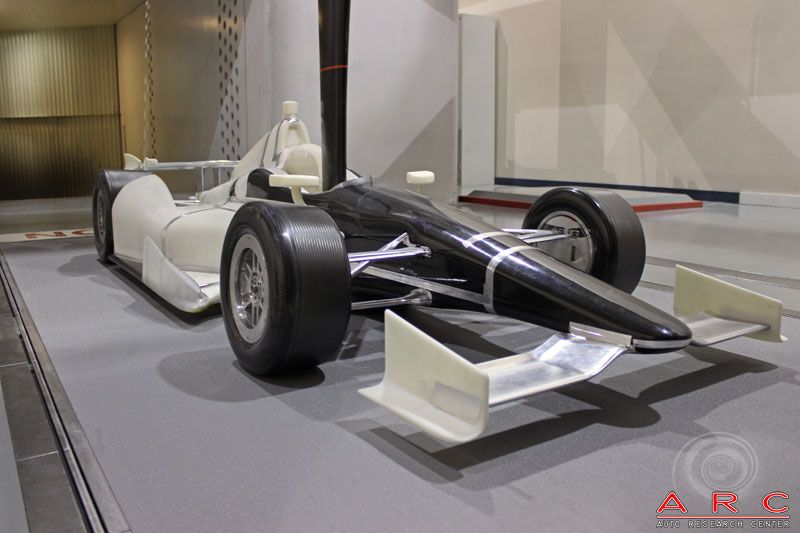
Why are we validating off car?
Cost, time, and accuracy. Validating a rear wing, or multiple in our case as we will be testing at least (2) of our profiles, costs us significantly less and still validates our analysis results. If a rear wing CFD analysis and wind tunnel correlate closely; then it can be assumed our full car analysis with similar mesh quality and setup parameters will correlate as well. It is also much easier and quicker to throw multiple wing profiles into a wind tunnel vs. an entire car or swapping trunks saving us time and money at the tunnel.
A rear wing only test also removes the vehicle in front of the rear wing from the equation. With the vehicle in front of the rear wing, it makes it more difficult to discern what the rear wing is producing as far as downforce and drag. It also muddies the data and introduces a source of error. Testing only the wings is a superior route to go for validating our CFD work without any question.
How will we be performing the testing?
We are working with ARC in Indianapolis to conduct all testing. They have a state-of-the-art wind tunnel with a sting specifically designed for wing testing. ARC works with IndyCar and NASCAR teams and will be helping us with the test procedure and data collection. We are testing the wings at 100 MPH airspeed and will be testing multiple angles of attack for each wing we test.
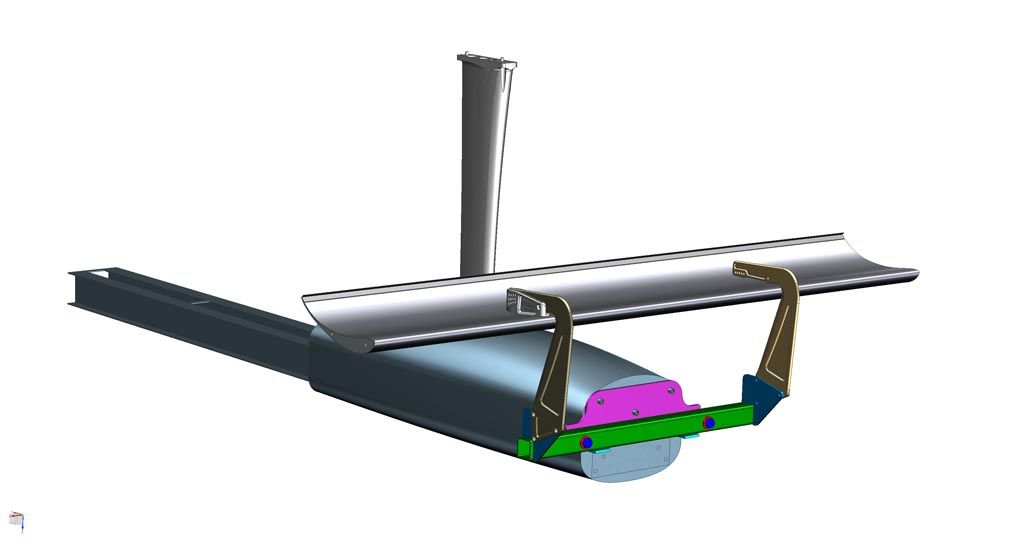
Verus Heads to the Wind Tunnel