We would like to give everyone a further, in-depth view of how we set up, run, and analyze our CFD cases here at Velox Motorsports. While we will not be giving away exactly how to set-up and run the analysis, we hope to give you enough information to instill confidence in our methodology and results. We decided there is no better way to show our skill set
First, we start working
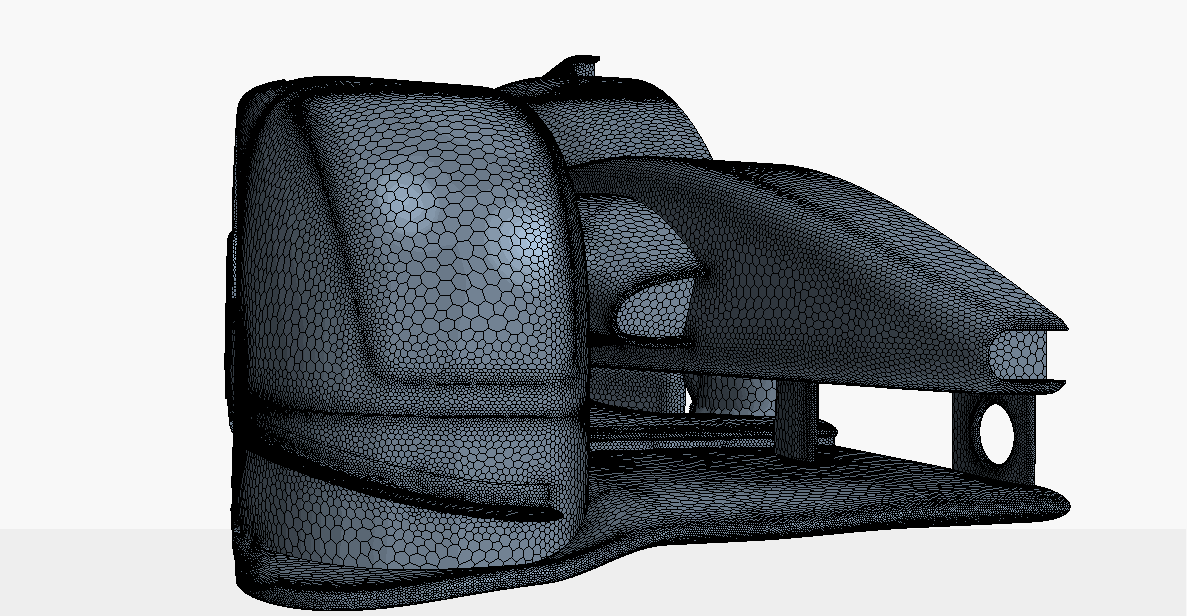
Next was placing the model into the CFD software and setting up the meshes. This step is very important and can become extremely
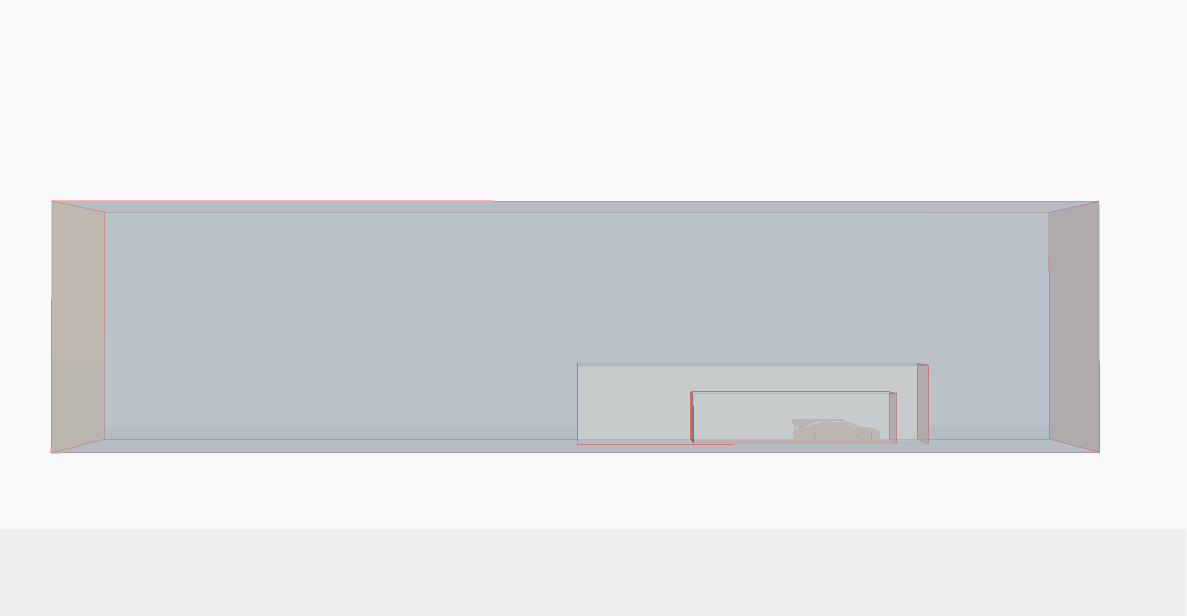
After the wind tunnel and refinement zones are nailed down, we begin setting up the vehicle’s surface mesh and volume mesh. Creating a proper mesh is not an easy process and has a direct effect on the accuracy of the case. If this is set-up incorrectly, results will not be accurate.
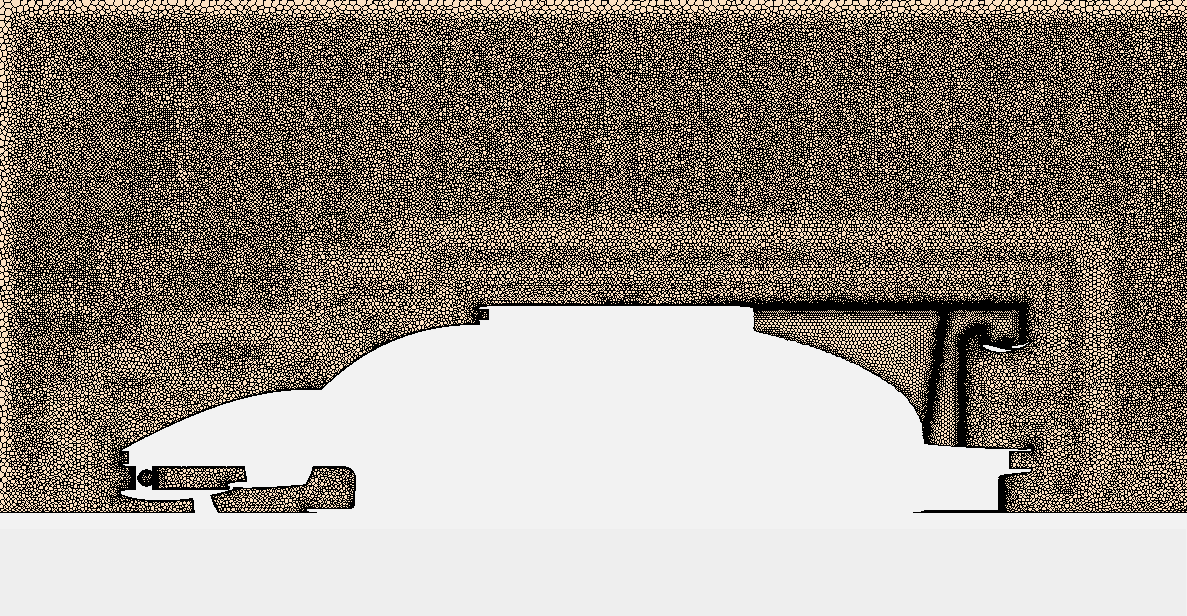
Next on the agenda is setting up the physics of the case. Of the analysis, this is likely the most difficult part to get correct. You have likely heard the phrase “the outputs are only as good as your inputs” and it certainly holds true here. When we run the CFD case, the car is not actually moving, it
To solve this, we used a steady-state solver with constant density. Depending on the analysis, we use a few different turbulence models. For this specific analysis, a realizable k-epsilon turbulence model was used. More physics setup takes place in the analysis but we can’t divulge everything :).
Before running the case we must setup stopping criteria or the analysis would run indefinitely. We generally watch for the coefficient of lift and the coefficient of drag to converge as our stopping criteria. This analysis took just under 25 thousand iterations to converge these values.
Post-processing is the final step in an analysis. We can now verify our numerical data with that
However, we are typically running analysis to see where we can make improvements for
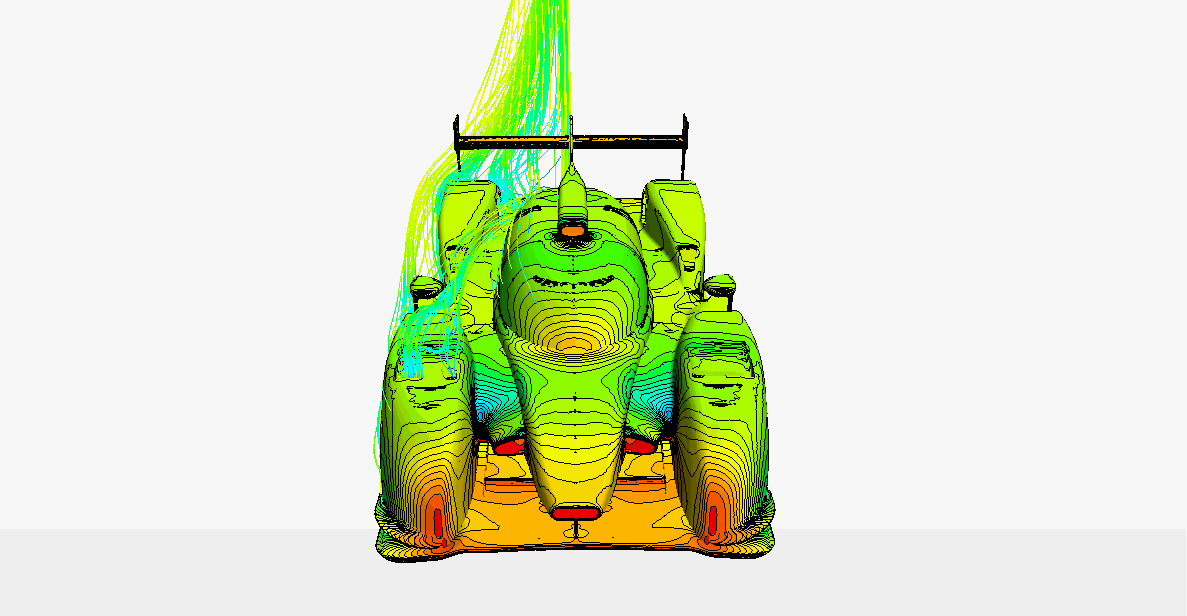
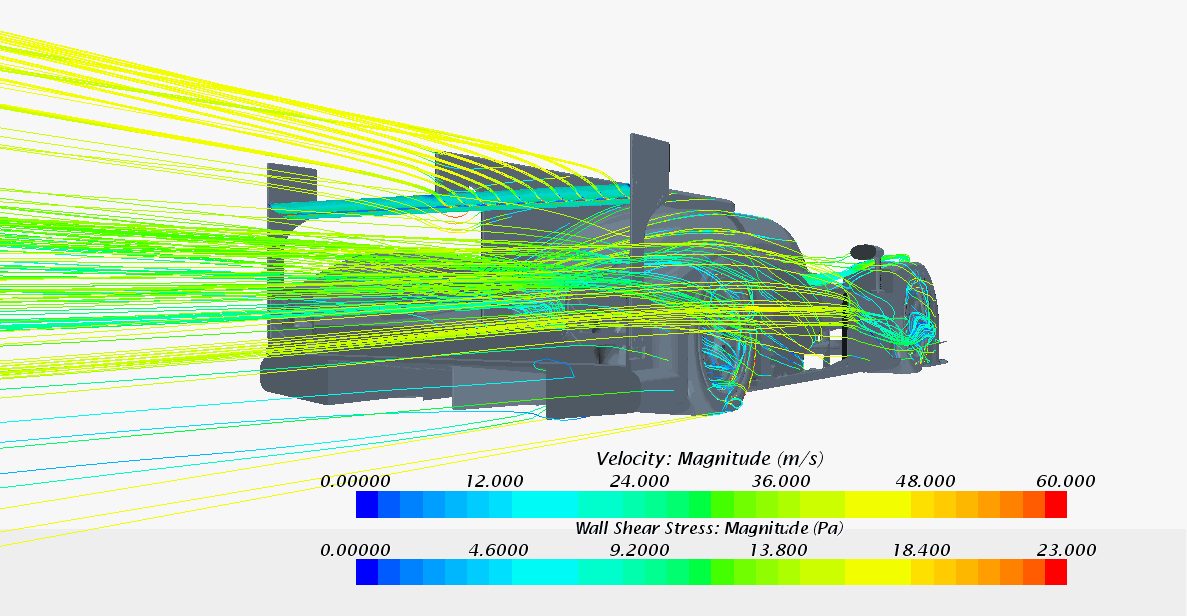
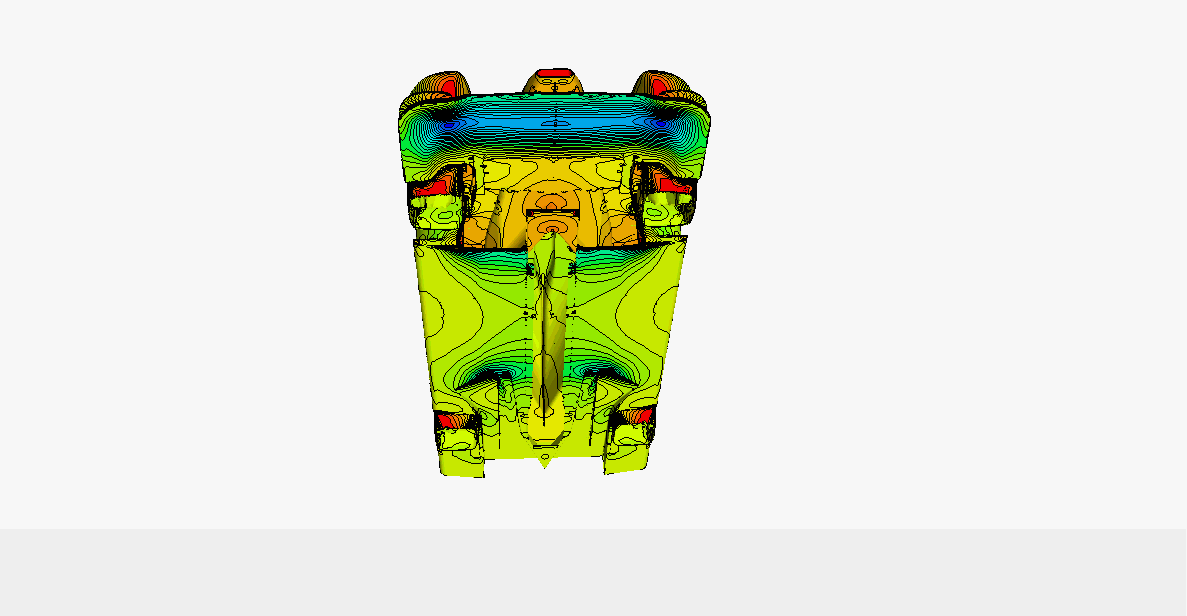
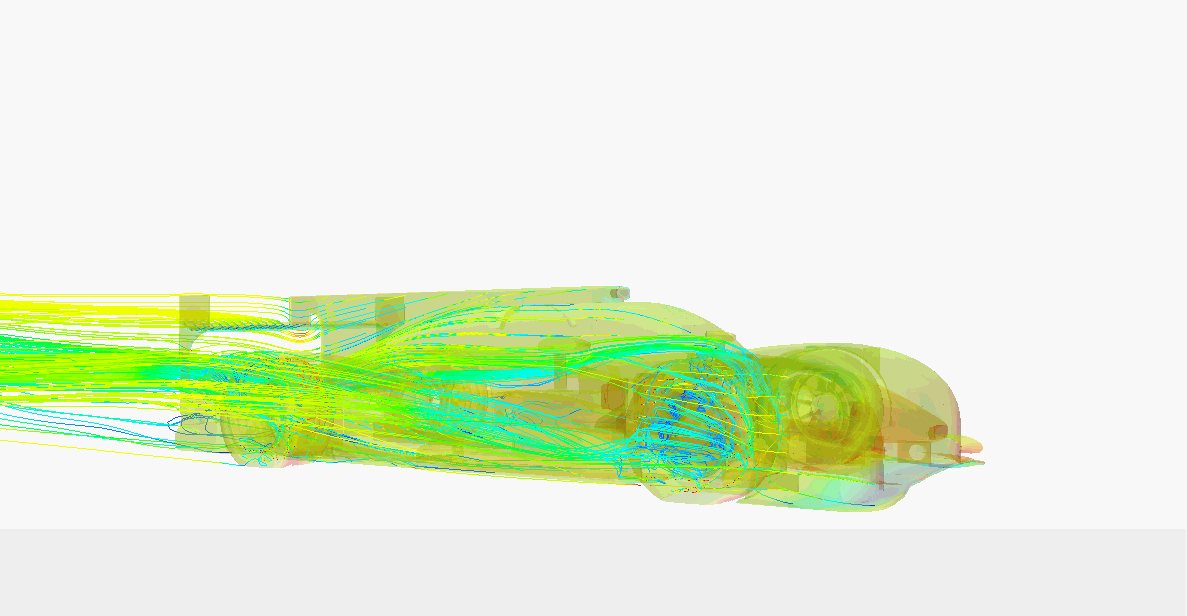
Even though CFD looks simple, it is far from it. A lot of times users become trigger happy and hit go on the CFD button well before he or she should. To setup, run, and analyze a study, users must not only understand the software thoroughly but also have a firm grasp on fluid dynamics and aerodynamics. Do not forget that basic hand calculations can verify if your answers are in the correct realm. Before CFD programs surfaced, all aerodynamics was done through hand calculations.
One Final Thought
A decent comparison for CFD software to something that is more readily spoken about on forums and in the aftermarket community would be dynamometers. We have all heard or said that dynos can read anything the user wants it to base on the input settings. The same is very true for CFD analysis. That is why at Velox Motorsports, we do our personal best to accurately
A Look Inside Verus Engineering CFD - Validation